Case Study
OEE Application for Modular Production Tracking
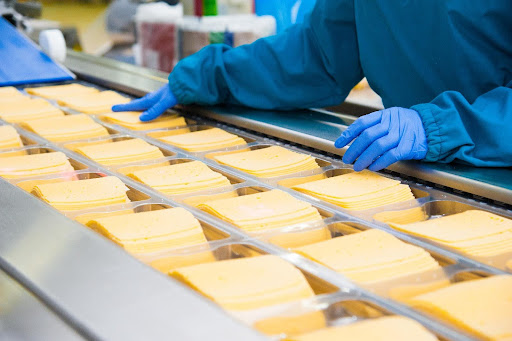
Industry
Food and Beverage
Company Size
Fortune 500
Facility Size
200+ Employees
Improve production performance within a short duration of implementation.
Challenges
A Fortune 500 Food and Beverage manufacturer faced difficulties in tracking production performance across five dynamic packaging and cartoner lines.
Frequent configuration changes were required to adapt to different product runs, with machines being relocated across lines or new machines being introduced. This lack of consistency made it nearly impossible to measure and monitor performance metrics effectively.
Solution
To overcome this challenge, mode40 implemented a modular OEE (Overall Equipment Effectiveness) solution:
- Machine-Level Tracking: Deployed OEE on each machine’s controller to monitor running, starved, and blocked states in real-time.
- Line-Level Tracking: Configured performance tracking based on physical locations instead of individual assets. Ethernet and power infrastructure were standardized across all line positions, enabling seamless plug-and-play functionality as machines were moved or replaced.
- Unique Identifiers: Ensured each machine was tracked individually using hardcoded identifiers, providing clear and accurate performance data regardless of location.
Outcomes
The mode40 solution delivered tangible results within a short time frame:
- Real-Time Problem Identification: Operators could quickly identify and resolve issues, minimizing downtime.
- Performance Improvement: Production performance increased by 9% within the first three months of deployment.
- Shift Optimization: An average reduction of two shifts per week was achieved, lowering labor costs and improving efficiency.
- Targeted Training: Data insights enabled customized operator training to address specific pain points and enhance performance further.
objective
About mode40
By aligning technology, people, and processes, mode40 unlocked immediate value for the customer, demonstrating the power of flexible, data-driven solutions in dynamic manufacturing environments.